SERVOsoft Revolutionizes the Sizing of Servo Systems
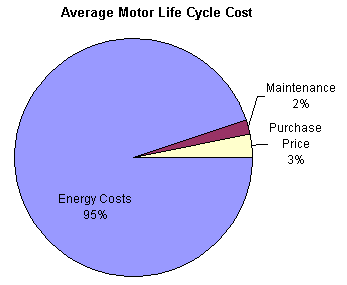
What is the need for a properly sized servo system?
What every customer and business wants - better performance and reliability at a lower cost. However, more often than not, a servo system is either undersized or oversized. An undersized system will fail to meet performance requirements, and in extreme cases, can overheat and damage components. Therefore, most engineers err on the side of caution and oversize since the numerous calculations can be complex and time consuming. However, an oversized motor is not a cost-effective solution. Larger motors require larger drives, and most often lead to larger infeed modules, filters, bleeders, cables, etc., which in turn require a larger cabinet enclosure to house the components. Over sizing has a ripple effect throughout the entire design. Usually larger components, be they motors, drives, gearboxes, etc., are higher priced than smaller units. Finally, an over sized design increases the long term operating costs as the design is inherently less energy efficient. And as shown in the Figure 1 chart to the right, energy costs dominate a motor's life cycle costs.
In summary, most engineers will over size because it is the easier and safer approach. However, over sizing increases the initial system cost as well as the ongoing operating cost of a servo system. So while over sizing is safe, it comes with significant costs.
What is the current method of selecting components?
Consider an engineer who is designing the servo system for a 3-axis gantry robot. The design must meet all the performance requirements including velocity profiles over a given cycle. The first phase of the sizing process is a collaborative effort with the mechanical engineering team. It begins with the mechanical design, which must be able to achieve the reach as well as sustain the forces created during the entire cycle. The gearbox and motor are then selected in an iterative process. Most sizing tools perform this task adequately. But this is where most sizing tools stop. The servo system engineer is then left to perform the remaining calculations manually to size the drive, filter, cables, bleeder module, etc. Typically, this is a very time consuming process, which applies rules of thumb to approximate the calculations. Rules of thumb are applied at various stages, from a constant gearbox efficiency over the entire speed range, to a linear torque constant (kt) for the motor, as well as the amount of bus stored energy and the overlapping of bus power requirements from each axis. Hence, rules of thumb are applied on top of each other. By the time the requirements of the infeed power module are defined, the design is based on layers of assumptions which can have an error of 20% to 50%.
Let’s look a little deeper at the power flow throughout the system. Most modern day servo systems are designed to be electrically coupled to share energy, minimize unused or oversized components, and reduce both initial hardware cost as well as operating costs by improved energy efficiency. Consider Figure 2 to the right which illustrates one possible configuration for a 3-axis gantry robot. For this example, each drive is connected to form one larger bus, and there is only one power supply connection which feeds all three axes. The internal bleeder in the Y axis drive is available to dissipate excess braking energy. Now consider what the engineer does today attempting to calculate the power flow for parallel moves - say the Y axis is decelerating while the Z axis begins to accelerate. This is virtually impossible to determine accurately by hand or by spreadsheet without extensive algorithms. Hence, the engineer resorts to more rules of thumb to approximate the loading each axis will actually draw from the supply, and then adds safety factors on top of the approximations to ensure the design will perform. The result is an oversized and more costly design.
Most sizing tools today are provided by the vendor for free. You can’t beat the price, but they tend to have a limited focus on only sizing the vendor’s product. That is, if the vendor makes motors, the focus is on selecting one of their motors, and does not adequately address drive or gearbox selection. With locked databases containing only the vendor’s products, scenario analysis is limited. Some users such as OEMs want to compare the same machine design with multiple vendors’ products. This is not possible without switching to other sizing tools. Additionally, these sizing tools do not properly address all major components in the system including drives, infeed, capacitor and bleeder modules, motors and gearboxes. And, very few consider bussed multi-axis designs. Consequently, when you add it all up, most free sizing tools look at a limited number of possible designs. These sizing tools are primarily marketing tools to help sell vendors’ products, which also assist in the sizing process.
How does SERVOsoft revolutionize the sizing of servo systems?
No guessing, no rules of thumb, just accurate results immediately. The gearbox efficiency is based on the actual efficiency at any given speed, and the motor model precisely calculates the non-linear torque-to-current conversion. Complete and thorough power flow calculations are handled with ease, including precise modeling of a floating bus. The user can click on any component, say the Z axis motor cable, the Y axis drive, or the system infeed cable, and the precise results are presented. In a few seconds, scenario analysis allows engineers to quickly and confidently assess the value of additional capacitor modules as it relates to energy efficiency and a lower cost solution as less bleeder capacity is required. And with open databases containing products from multiple vendors, benchmark one vendor against another in a matter of minutes.
SERVOsoft is complete, accurate, and immediate. In large organizations such as OEMs who manufacture hundreds or even thousands of machines and robots per year, the cost savings and improved customer value are multiplied through better and efficient designs. In these organizations, the value of SERVOsoft is leveraged significantly. By dramatically reducing the servo system design process by as much as 50% from weeks to days, design cycles decrease, products reach the market sooner, and resources are freed up to work on other projects. All the while, the customer gets a better performing, more reliable and efficient machine. Win, win, and win.